We are now at a stage where it is all about the details. Lots of little individual parts and sub-assemblies being finalised and coming together, ready for the final assembly of the ride. We’re obviously still not saying who it is for as we will be unveiling that at EAS in Barcelona, stand 833 on September 20-22nd and the team will be on hand to answer any questions.
Progress is still rapid and by next week, we will have big progress to show with the cars being fully up and running and getting close to the return of the passenger tubs all finished and ready to go. In the meantime, here are some of the detailed shots that we as a team of engineers love and most people never even notice, when they step on to enjoy a theme park ride.
The sub-assemblies are all now completed to our BS EN 1090 ensuring all the parts are welded correctly and the parts we use completely traceable to their source.
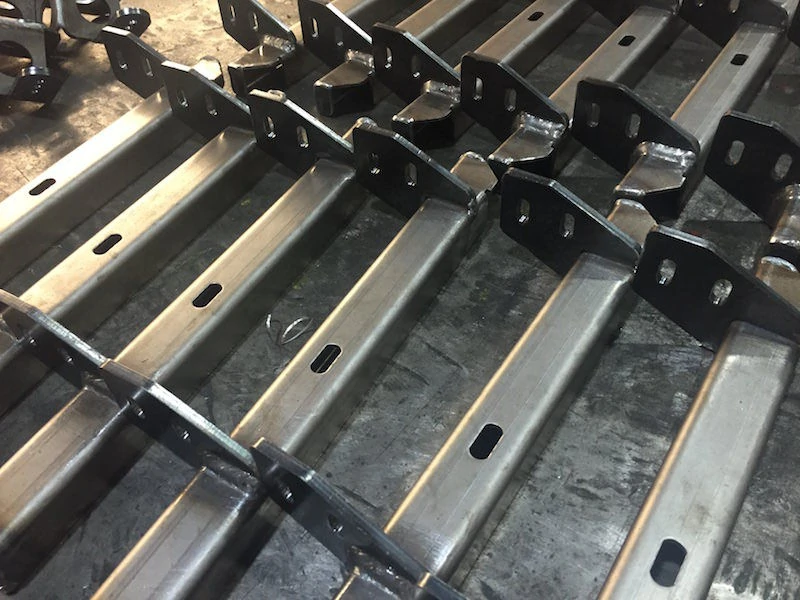
The new spray shop comes in very handy when you have to lay out over 100 track jointing plates to be sprayed. Again, most people would never see these, but we believe that every detail matters when you are creating well built, long-lasting rides. We love the fact that they match the colour and spec of the rails perfectly!
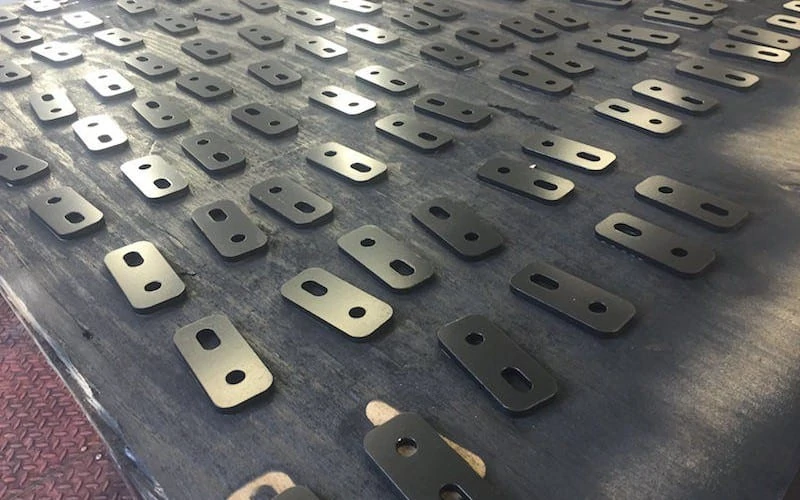
The next fabrication job is the Transformer Control Box. It’s a relatively simple thing made up of laser cut panels. But making it right, ensures that the important parts it contains are safe and well protected from dust, moisture and interference.
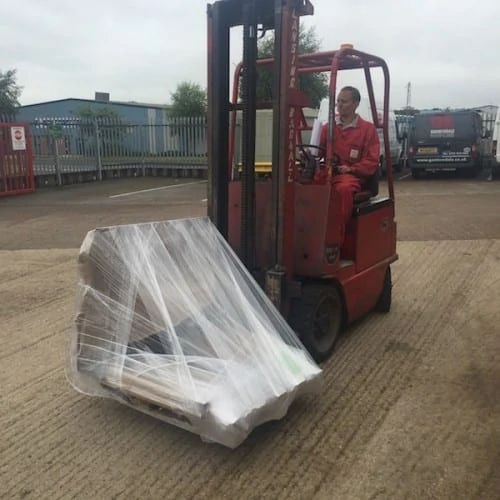
The rails are all completed and we even manufactured a simple cage to make it easier to transport them.
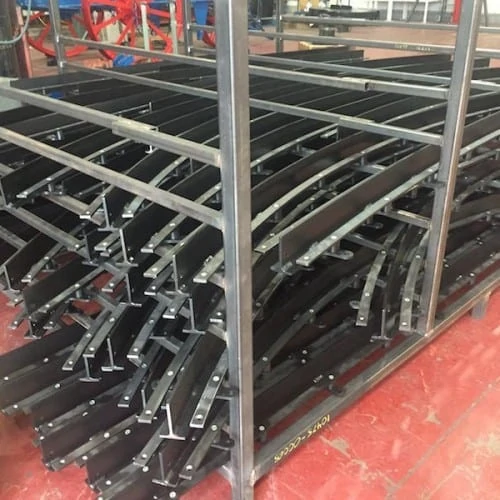
And the innards of the control box are nearing completion too. We’ve just had a delivery of all the final parts for this, so it’ll be finalised later today too.
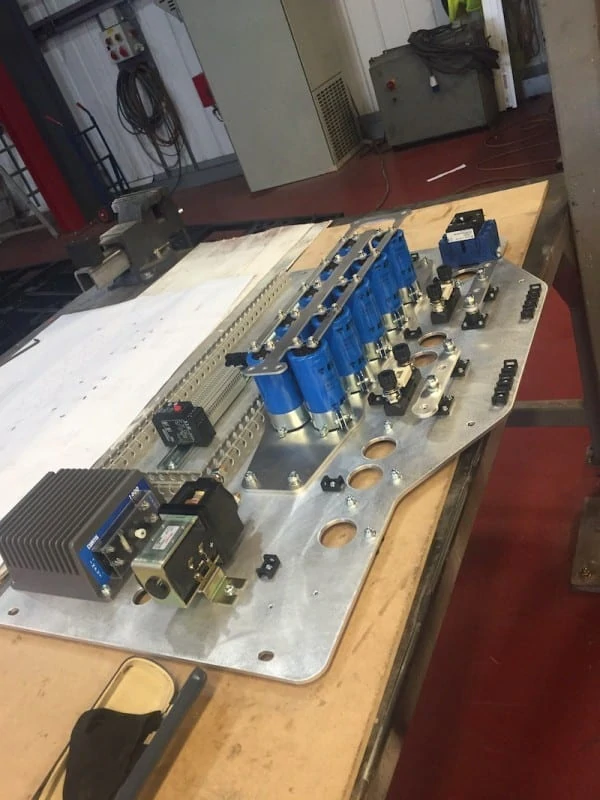
So as soon as the parts arrive, they are pressed into action and only three hours after the parts arrive, the Transformer Control Box, which is already tacked in place is being fully welded together. There’s a few things to note here. The box is tacked at intervals to get the shape right. It’s also marked up in 150mm lengths per side, so it is welded in short-runs. This helps reduce any warping with the heat of the welding. It’s also cross braced to retain as much of the structural integrity as possible whilst it’s being welded. All simple steps, but again little details that matter to us.
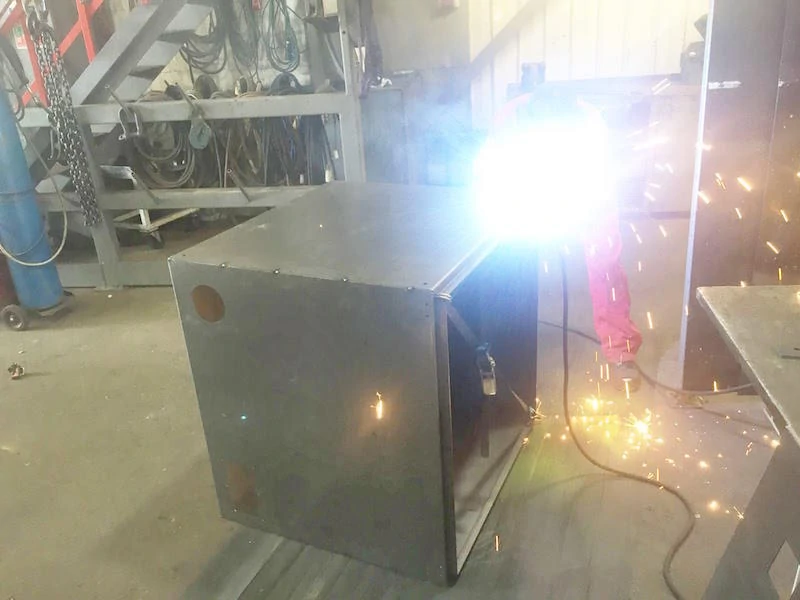